Currently, one of the main components of solid waste produced daily by humans is plastic. Major sectors such as healthcare, building construction, automobile, and packaging industries utilize plastic for their process [1]. Owing to its widespread use, low cost and growing population, commercial plastic production has increased. According to global statistics, approximately 459.75 million tons of plastic were manufactured worldwide in 2023 [2]. If current development trends continue, it is estimated that the world’s primary plastic production will reach 1,100 million tons by 2050 [3]. Owing to the massive production and usage of plastics, there has been a great increase in the accumulation of plastic waste every year. During the past 60 years, an estimated 8.3 billion tons of plastic waste were produced, among which only 9% has been recycled, while the remaining 79% has been disposed of in landfills, and the remaining 12% has been incinerated [1], [4]. These particular data indicate that the percentage of waste plastic dumped in landfills is massive and that more space is available and that degrading plastic waste takes billions of years naturally [5]. The degradation of plastic takes place very progressively because of the molecular interactions between hydrogen, carbon, and other elements, such as nitrogen, chlorine, and others, which make plastics very strong. There may be serious problems when waste plastic is thrown into landfills [6]. Long-term risks of disposing plastic waste in landfills results in long degradation period, potential leaching of poisonous chemicals, emission of greenhouse gases, and the resulting growth of microplastics that damage ecosystems [7]. The difficulty of recycling plastic waste lies in the high costs because of a need for extensive manual labor to sort and clean diverse plastics, which are compound different resin types, colors, and levels of transparency. The sequential separation process is highly essential to ensure the quality of recycled materials [8]. Since there is a growing demand for plastics, the researchers are focusing on exploring the ways to use the energy sources including natural gas, coal, and petroleum which are the vital raw materials in the production of plastic. Recycling has been evaluated as another option for managing waste plastic to decrease landfill discharge. Returning to the previous data, the recycling rate remains the lowest [9]. Plastics that are colored or dyed have reduced market value. Recycle process prefer transparent plastics mostly because they can be easy to colour and transform into new products, giving them more flexibility [10]. Plastic recycling can help minimize some amount of waste, and a more effective and long-term solution has been found. Because of the increased need for plastics, many scholars are interested in discovering and developing possible energy capitals, such as gas, coal, and petroleum, that are used to make plastic [11]. Wind power, solar energy, hydropower technology [12], and geothermal energy are some of the newest energy options that have been investigated. Recently, waste-to-energy conversion has been shown to be a smart strategy to fully utilize waste to fulfill rising energy demand. Converting waste plastic with valuable energy can be performed, as these plastics are derived from a petrochemical source and have a large calorific value.
Today pyrolysis technique is the main process used for minimizing waste plastics, which have recently become popular [13]. Pyrolysis is a recycling technique that involves the conversion of higher-molecular-weight organic polymers by thermal or catalytic decomposition without burning polymer waste. The ability to convert thermoplastic waste and thermoset polymers into high-quality oils and chemicals is the main advantage of pyrolysis technology [14], [15]. Additionally, it can be used to treat all types of waste, such as unsorted waste, without releasing harmful compounds into the surrounding air. This review summarizes the process of pyrolysis of important plastic waste, including PET, HDPE, LDPE, PVC, PS, PP and mixed plastics [16], [17].
Pyrolysis is the process of the thermal degradation of long-chain polymers to simpler and less complex compounds. This technique requires a lot of heat for a short time under anaerobic conditions [18]. Oil and char are the two important products obtained after pyrolysis and are essential for industry and refineries [19]. This technique also has the advantage of creating a large volume of oil (up to 80 wt%) at a decent temperature (approximately 300 °C to 500 °C). Additionally, pyrolysis is highly flexible because its parameters can be altered to improve the production yield. The oil obtained can be utilized in a variety of applications, such as furnaces, boilers, diesel engines, and turbines, without any need for additional treatment or upgrading [20].
Unlike recycling, the pyrolysis technique does not contaminate the water and therefore is classified as a “green technology”, and its byproduct has adequate calorific value to compensate for the overall energy requirements of the pyrolysis treatment plant. Because this technique does not require a rigorous sorting procedure, the process treatment is significantly easier and more flexible than conventional recycling approaches are [21].
Many factors in the plastic pyrolysis process require attention to improve the liquid oil output and improve the oil quality. Temperature, reactor type, pressure, residence time, various catalysts such as ZSM-5 zeolite, silica, red mud, fluidizing gas type and flow rate are significant factors [22], [23]. A pyrolysis reactor is often set up in an open space, and the reactor is filled with different types of plastics in known amounts. Air is removed from the reactor via an external vacuum pump or completely fills the waste plastic to avoid cross contamination, and then the reactor is heated. A schematic of the pyrolysis reactor is shown in Figure 1 [24].
A schematic set up of the plastic pyrolysis process
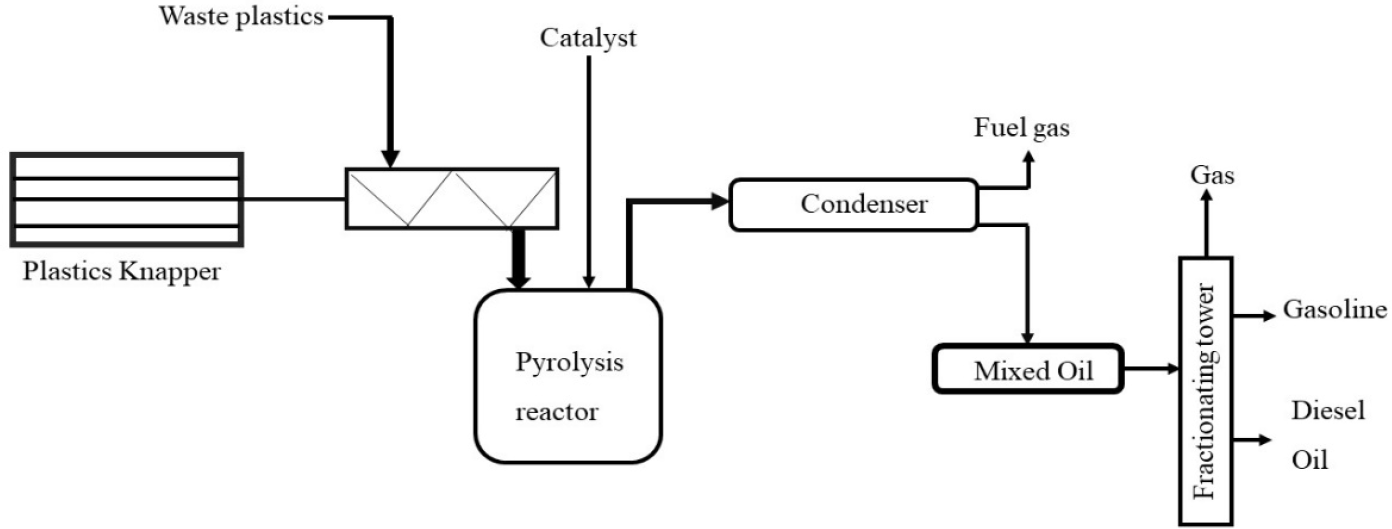
It is a common method of pyrolysis. It requires an extended duration of time, and the rate of heating is moderate. Slow pyrolysis involves pyrolyzing feedstock at 400-500 °C at rates ranging from 0.1-1 °C per second. Slow pyrolysis takes approximately 5 to 30 minutes to complete. Slow pyrolysis results in the formation of carbon-containing char. During pyrolysis, gaseous and liquid products are generated, although in small amounts [25].
Fast pyrolysis itself describes the rapid heating of feedstock materials to temperatures ranging from 800 to 1300 °C. The temperature increases at a rate of 10–200 °C for only a limited duration of 1-10 seconds. This fast pyrolysis can be used for oil products because it produces more liquid oil. The product contains 60 to 70% biofuel derived on thermal decomposition of plastics in to liquid hydrocarbons, 14 to 20% solid biochar, and 11 to 21% non-condensable gaseous material [25].
This biofuel is derived from the thermal decomposition of plastics into liquid hydrocarbons.
Flash pyrolysis is also called very rapid pyrolysis and requires a few seconds to react. The temperature needed for flash pyrolysis is very high, and the heating rate should be 1000 °C per second. This technique yields a high output of oil with less water content and has a liquid‒oil efficiency conversion of 70% [25].
Plastics are available in many different compositions, most of which are identified via proximate analysis. The proximate analysis indicates its composition, such as volatile matter, moisture content, fixed carbon content, and ash content. The main properties that contribute to and hinder the formation of waste plastic oil are ash content and volatile matter. The ash content in plastic waste can lead to gaseous productivity and charge generation [26], [27], [28]. Table 1 shows the brief proximate analysis of different plastic types.
Polyethylene terephthalate (PET) has grown in popularity as a packaging material for diverse edible commodities, primarily drinks such as mineral water, juice containers, and soda bottles. Greater volume, pressure-resistant containers, and light weight are important properties that make them ideal candidates. PET is used in electrical and optical industries for applications such as electrical insulation, photographic film, X-ray, printing sheets, and magnetic tapes; its ubiquitous use has led to the generation of PET waste in landfills. Currently, PET waste handling procedures include recycling; however, large amounts of PET waste can increase transportation expenses, and recycling PET is inefficient and uneconomical because of different grades and colors. As a result, other methods of PET retrieval, such as pyrolysis, have been investigated, and the end product has been evaluated by numerous scientists [35], [36].
Cepeliogullar and Putun examined the pyrolysis of PET to create oil in a fixed reactor at approximately 500 °C. In that experiment, the rate of heat was approximately 10 °C/min, along with a sweeping gas, which was nitrogen. The oil production was significantly inferior to that of the gaseous product. The oil recovered was 23.1 wt%, whereas the gaseous product was 76.9 wt%, with zero solid residue remaining. Table 1 shows the low liquid yield based on the proximate analysis; it also reveals approximately 86.83% fewer volatile constituents of PET than other varieties of plastics, but the unstable compounds are mostly above 90%. Unfortunately, according to the gas chromatography‒mass spectrometry (GC–MS) results, the oil composition included benzoic acid, which was present in nearly 49.93% of the samples. The acidic nature of the pyrolyzed oil was negative because of its corrosive nature, which reduced the quality of the fuel. Furthermore, benzoic acid, which is a basic elevation that can lead to clogging in pipelines and heat exchangers, necessitates careful monitoring if it is used at an industrial scale [37], [38].
The volatile matter of every plastic is very high, and the ash content is considerably low, which makes plastics good candidates for significant oil production through the pyrolysis process.
Fakhrhoseini and Dastanian [39], on the other hand, discovered that a significantly greater amount of oil liquid was produced at very similar heating rates and operating temperatures. The liquid oil yield was 39.89 wt%, the vapor yield was 52.13 wt%, and the solid precipitate content was 8.98 wt%. As a result, the oil liquid output from the pyrolyzed PET was in the range of 23-40 wt%, whereas the vaporous yield was in the range of 52-77 wt%. According to these findings, polyethylene terephthalate may be the best polymer for pyrolysis if gaseous products are preferred, such as providing energy to keep the container at the optimum temperature.
Plastic proximate analysis
Plastic types | Backbone | Fixed carbon (in wt%) | Moisture (in wt%) | Ash (in wt%) | Volatile (in wt%) | Ref. |
---|---|---|---|---|---|---|
Polyethylene terephthalate (PET) | 7.77 13.17 |
0.46 0.61 |
0.02 0.00 |
91.75 86.83 |
[1] [29] |
|
High-density polyethylene (HDPE) | 0.001 0.03 |
0.00 0.00 |
0.18 1.40 |
99.81 98.57 |
[30] [29] |
|
Polyvinyl chloride (PVC) | 6.30 4.44 |
0.80 0.74 |
0.00 0.00 |
93.70 94.82 |
[31] [29] |
|
Low-density polyethylene (LDPE) | 0.00 _ |
0.30 _ |
0.00 0.40 |
99.70 99.60 |
[29] [32] |
|
Polypropylene (PP) | 1.22 0.16 |
0.15 0.18 |
3.55 1.99 |
95.08 97.85 |
[29] [29] |
|
Polystyrene | 0.12 0.20 |
0.25 0.30 |
0.00 0.00 |
99.63 99.50 |
[27] [32] |
|
Polyethylene (PE) |
0.04 |
0.10 |
0.99 |
98.87 |
||
Polyamide (PA) or Nylons |
1.12 | 0.00 | 1.01 | 97.88 | ||
Acrylonitrile Butadiene Styrene (ABS) |
0.69 | 0.00 | 0.00 | 99.78 | [29] [33] [34] |
|
Polybutylene terephthalate (PBT) |
2.88 | 0.16 | 0.00 | 97.12 |
High-density polyethylene (HDPE) is a lengthy linear polymer chain with a maximum degree of little branching and crystallinity, resulting in good strength. High-density polyethylene is frequently utilized in the production of detergent containers, oil containers, toys, milk bottles and other products because it has high tensile features. Various applications that use HDPFs account for approximately 17.6% of the plastic waste category - the third most prevalent type of plastic found in MSW.
High-density polyethylene waste has significant potential for use in the pyrolysis technique because it may create a maximum yield of liquid depending on the setup settings. Several investigations on high-density polyethylene pyrolysis under various operating conditions have been undertaken to explore the product yield produced (Table 2).
Conventional fuel and HDPE pyrolytic oils are compared
Oil types | HDPE properties of pyrolytic oil [40] | Properties of conventional fuel [19] | ||
---|---|---|---|---|
Boiling point in °C | Cv in MJ/kg | Boiling point in °C | Cv in MJ/kg | |
Gasoline | 40-200 | 43.4-46.5 | ||
Diesel | 82-352 | 42.9 | 150-390 | 42.8-46.2 |
Kerosene | 150-300 | 43.0-46.2 |
Ahmad and his team [41] investigated the pyrolysis of high-density polyethylene in a steel reactor (microsteel reactor), and the pyrolysis temperatures ranged from 300–400 °C, with a heating rate of 5–10 °C per minute. As a fluidizing medium, nitrogen gas was used for the experiments. It has the highest maximum conversion at 350 °C. The dominant liquid yield produced was 80.88 wt%. The residue of the solid was relatively stable at 300 °C (33.05 wt%), but then it decreased to 0.54 wt% at the highest temperature of 400 °C.
Kumar and Singh [40], on the other hand, carried out pyrolysis studies of HDPE in a reactor (semibatch reactor) at temperatures ranging from 400 to 550°C. The gaseous product (24.75 wt%) and the largest liquid oil yield (79.08 wt%) were produced at 550°C, but wax started to form in the product fraction at extremely high temperatures ranging from 500 -550 °C. After pyrolysis, brownish-dark oil with no apparent remnants formed, and its boiling point ranged from 82 to 352 °C. It is a blend of diverse oil components, such as diesel, kerosene and gasoline, that resemble the same qualities of traditional fuel; on the other hand, the presence of sulfur present in the high density of the pyrolytic oil is lower than 0.019%, which is cleaner for the environment.
In addition, Marcilla et al. [42] investigated high-density polyethylene pyrolysis at 550 °C in a reactor (batch reactor). The oil–liquid content was 84.7% by weight, whereas the gaseous product output was approximately 16.3 wt%. The study showed that larger oil liquid levels could be achieved at higher temperatures; however, there is a constraint that must be recognized. Because this technique results in the highest degradation temperature, the liquid oil yield can be reduced because of the high temperature while increasing the amount of the vaporous product. Mastral et al. [43] performed high-density polyethylene pyrolysis in a reactor (fluidized bed reactor) at 650 °C and reported that the oil output was approximately 68.5 wt%, and the vaporous product was 31.5 wt%. This signifies that the liquid was then converted to gaseous vapor when heated intensively above 550 °C.
When other thermoplastic resins, such as polystyrene, polypropylene, and polyethylene, are used, they can be made softer by heating at higher temperatures, resulting exclusively in oil. Polyvinyl chloride (PVC) is a unique plastic that is composed of 57% chlorine (produced from industrial-grade salt) and 43% carbon (C). Because of its chlorine characteristics, PVC has great fire resistance and is therefore ideal for electrical insulation. PVC is a versatile material due to its adaptability to a wide variety of additives. The PVC is extensively used in cable and wire insulation, food foils, boots, window frames, hospital instruments, blood bags, vehicle components, packaging, bank cards, synthetic leather, and other products. Despite its many applications, research on PVC-related pyrolysis has been minimal because of the emission of toxic chemicals when subjected to high temperatures.
Miranda et al. [44] conducted the pyrolysis of PVC in a batch reactor at temperatures ranging from 225 to 520 °C and a heating rate of 10 °C per minute. The amount of oil liquid formed was not relatively high, ranging from 0.45 wt% to 12.79 wt% when the temperature increased. The amount of char deposited is considerably greater than the amount of oil liquid collected, reaching 19.6 wt %. The major hydrogen chloride product of the experiment was found to have the greatest yield of 58.2 wt %. When heated considerably, hydrogen chloride becomes poisonous and corrosive, causing damage to machine components. This is one of the primary reasons for the closing of the pyrolysis processing facility in Ebenhausen, Germany [44].
As the production of oil liquid was minimal, polyvinyl chloride was considered inappropriate for the pyrolysis process. Moreover, the amount of polyvinyl chloride material gathered in municipal solid waste was low, accounting for 3% less than that in the waste plastic group, which was highly restricted [45]. Furthermore, the concentration of chlorine in pyrolyzed liquid containing chlorobenzene and the emission of hazardous products such as hydrogen chloride may even be environmentally hazardous. To address this, a PVC dechlorination procedure was necessary to lower the chlorine concentration of the liquid oil. This method can be accomplished in a variety of ways, including catalytic pyrolysis, stepwise pyrolysis and pyrolysis with adsorbent materials combined with a polyvinyl chloride sample [46]. As a result, the pyrolysis of polyvinyl chloride requires an extra cost when an additional dechlorination process is performed, which is a drawback.
Low-density polyethylene (LDPE) has greater branching than high-density polyethylene, which results in less intermolecular force and consequently a lower hardness and tensile strength. Moreover, LDPE is more ductile than HDPE because side branching makes the framework less crystal-like and relatively effortless to shape [47]. LDPE has good water resistance and is thus commonly used in shopping bags, packing, foils for wrapping, trash bags, and many other applications. These commodities remain widely utilized in our everyday lives, and as a result, LDPE material is the 2nd largest municipal solid waste after PP [48]. The pyrolysis of LDPE plastics into oil has recently attracted considerable interest from researchers as a method for reducing waste plastic and recovering energy.
Bagri and Williams [49] experimented on LDPE plastics via a fixed-bed reactor at 500 °C and heated them at a rate of 10 °C per minute. The experiment was carried out for 20 minutes using nitrogen as the fluidizing gas, which produced more 95% liquid with less char and gas production. Marcilla et al. [42] obtained a relatively high oil liquid output of 93.1 wt% when pyrolysis was carried out in a reactor (batch reactor) at 550 °C but at a low heating rate of 5 °C per minute.
Uddin team [50] conducted and studied the pyrolysis of LDPE at a lower temperature of 500 °C. The liquid yield produced via a batch reactor at 430 °C was approximately 75.6 wt%. When the same type of reactor was used at 450 °C, Aguado et al. produced a greater yield (74.7 wt %) than did the previous study. Moreover, even at lower temperatures, liquid oil production might be improved by applying pressure to the reactor throughout the process [51]. Onwudili et al. [52] demonstrated this study using a pressurized batch reactor. For LDPE pyrolysis at 425 °C, 89.5% oil, 10% gaseous products, and 0.5% char were collected from experiments. This shows that the pyrolysis product composition is impacted by pressure.
Compared with HDPE, PP does not melt at temperatures lower than 160 °C. Polypropylene (PP) is considered a saturated polymer that has a linear hydrocarbon chain that is thermally resistant and chemically stable. PP is a better choice for plastics since it has a lower density than HDPE does and is also hard and stiff. PP corresponds to approximately 24.3% of the waste plastic group, which contains a great number of plastics in municipal solid waste [18]. PPs have been used in different kinds of applications, such as office folders, flowerpots, furniture, storage boxes, pails, carpets, and car bumpers. The increasing need for the use of PP in everyday life results in the rate of PP waste exponentially increasing each year; thus, pyrolysis is one of the techniques. According to these findings, Polyethylene terephthala that may be utilized for the recovery of energy. Various studies have been conducted in the field of the pyrolysis of waste PP under different conditions to determine the production of oil and other components [53].
Ahmad et al. [41] pyrolyzed PP using a micro steel reactor at a temperature between 250 °C and 400 °C. This experiment revealed that at higher temperatures up to 300 °C or higher, the oil yield was 98.66%. When the temperature increased to 400 °C, the total conversion decreased to 94.3%, and the amount of solid waste increased from 1.3 to 5.71 wt%. Sakata and team [54] examined the pyrolysis of PP at temperatures greater than 370 °C. They reported greater oil yields of 80 wt%, 6.61 wt% gaseous residues, and 13.2 wt% residual waste. Fakhrhoseini and colleagues obtained a relatively high oil yield of approximately 82.1 wt% while performing PP pyrolysis at temperatures greater than 450 °C. Nonetheless, increasing the temperature above 500 °C merely lowered the liquid output [39]. Demirbas [55] demonstrated this by performing pyrolysis of PP at a high temperature of 745 °C in a reactor, yielding 48.81 wt% oil, 1.6 wt% char, and 49.6 wt% gaseous.
Polystyrene (PS) is considered to be a lengthy hydrocarbon chain that contains a phenyl group attached to a carbon. PS is made from a styrene monomer derived from liquid petrochemicals. Naturally, polystyrene is colorless, but colourants can be added to make it colorful. Owing to its heat resistance, good strength, durability, and light weight, this polymer is ideal for use in a wide range of industries, including food packaging, construction, electronics, medical appliances, and toys [56]. A wide range of applications is evident for the large amount of polystyrene that is generated annually in municipal solid waste. However, polystyrene is not found in the recycling package but includes only glassware, newspapers, and certain types of plastics in the recycling bins. The majority of people throw foam food packaging into regular waste rather than recycle it, even though plastic waste has been classified [57]. The low density of polystyrene foam makes it difficult to collect and recycle economically. Because of these issues, the pyrolysis process is the most effective approach for converting polystyrene to potentially valuable oil products; otherwise, polystyrene waste landfills can cause environmental issues [56].
Onwudili et al. [52] conducted pyrolysis of PS in a pressured autoclave chamber at a temperature of 300–500 °C for approximately 1 h. The heating rate was 10 °C per minute, and the testing pressure ranged from 0.3 MPa to 1.61 MPa. They noted that the pyrolysis of PS provided a high oil yield of approximately 97 wt% at the optimal temperature of 425.0 °C. The highest volume of fuel generated was approximately 2.6 wt%.
Liu and colleagues [58] also obtained a high yield of liquid oil when polystyrene plastics were pyrolyzed in a bed reactor at 450–700 °C. Approximately 98.7 wt% of the highest amount of oil was produced at 600°C, and oil production was found to be high at lower temperatures of 455 °C, with 97.5 wt% and 1.1 wt% varying only. According to Demirbas’ observation, when the pyrolysis of polystyrene occurred at 580 °C in the reactor, the oil yield was reduced to 89.6 wt%. Thus, the continuation of pyrolysis at a high temperature of more than 520 °C does not yield a high liquid output [55].
Since pyrolysis does not need the thorough separation of plastics, it has an advantage over conventional recycling. In contrast to recycling, which frequently necessitates exact separation because various polymers are incompatible (for example, PVC contaminating PET), pyrolysis may handle mixed plastic trash without requiring such meticulous sorting [59].
A small amount of polyvinyl chloride contamination in PET recycling is one example, which has the potential to ruin the PET resin entirely, turning it rigid and brown, demanding recycling [60]. These findings illustrate that the recycling process is so vulnerable to contamination that all polymers must be organized on the basis of polymer variety, color, and opacity. The pyrolysis method, on the other hand, appears to be much more efficient since oil might be created from combined polymers in stock. Various scholars who have researched mixed plastic pyrolysis have observed this [61].
The experiment conducted by Kaminsky and colleagues [62] involved mixed plastic waste, which was gathered from German households and contained 25% polystyrene and 75% polyolefins. The occurrence of chlorine demonstrated that a minimal quantity of the required PVC components remained in stock after the separation step (only approximately 1 wt%). They employed a fluidized reactor at a temperature of 725 °C, obtaining 48.3 wt% oil.
Donaj and colleagues [63] explored the prospects of pyrolysis for polyolefin mixed resins. These mixed polymers were made up of 75% LDPE, 30% HDPE, and 24% polypropylene. The experiment was conducted inside a bubbling fluidized furnace at 650–730 °C. The results revealed that the amount of liquid generated was much greater at temperatures lower than 650 °C, with an average value of approximately 48 wt%. This oil mixture, on the other hand, constituted 52% of the heavy portion, including more oil, carbon black, and wax.
Compared with mixed plastic pyrolysis and single plastic pyrolysis, mixed plastic pyrolysis yields a lower yield (> 50 wt%). However, in terms of liquid oil composition, the quality of the oil formed was similar to that of single plastic pyrolysis, making it suitable for further handling in petrochemical factories [26].
The economic cost of producing polymer liquid oil is influenced by several variables, including capital expenditure, fixed expenses, manufacturing costs, and associated expenses. While analyzing the return on investment (ROI) important factors like including the types of plastics used, transport cost, plastic separation from municipal solid waste, labor, cost of maintenance, research facility cost, employees, rent, calorific value of waste, power and thermal generation improved the efficiency of the pyrolysis components and the energy used in power generation should be considered Click or tap here to enter text.[64][65]Click or tap here to enter text.. Each stage costs between $65 and $400 per tonne in the United States. The labor cost has a noteworthy effect on Return on investment (ROI), which is defined as profit before taxes divided by ‘total capital invested’ [66]. A technoeconomic examination of a combined reactor of mixed polymers in the Netherlands revealed that a bubbling fluidized bed (BFB) working at a temperature of 740 °C has an ROI of 21.6%, a rotating cone reactor functioning at a temperature of 625 °C has an ROI of 14.2%, and an ROI of 295% is obtained in a circulating fluidized bed (CFB), which runs at a temperature of 840 °C. Because the recovery of energy is not entirely perfect, a low reaction temperature makes it useful in both environmental and economic aspects [66]. The capital investment for a CFB pyrolysis plant’s annual production capacity of 50 kilo tonne/year is projected to cost approximately 7.84 and 11.2 million U.S. dollars [66]. An experiment conducted by Shelley and colleagues demonstrated that a 14% ROI is obtained by fixing the tilting price between $36 and $45, with a reactor loading rate of 300 tonnes per day [67]. Salem et al. [68] investigated the thermochemical transformation of plastics in the United Kingdom. The study revealed that hydrocracking had a greater return on investment (ROI) than pyrolysis at lower temperatures in the range of 155 kilo tonnes each year; the return on investment (ROI) was 53%, whereas the ROI with lower-temperature pyrolysis was 43%. Therefore, hydrocracking results in a greater net value and pretax earnings than does lower-temperature pyrolysis. Arena and team [69] studied the technoeconomics of a fluidized gasification bed unit, which was again included in the transformation of waste plastic into power in Italy. According to the analysis, with a 23.7% power conversion efficiency, the return on investment is 8.4% when the plant expenses are 4.78 k€/kWe and the running expenses are 0.75 (k€/y)/kWe. All variable expenses are included in the operational costs.
Plastic is a versatile material as it can be used to produce commodities in all shapes and sizes for various usages. Waste generated from the plastic cause nuisance by polluting land, clogging drain and can survive in the landfill for generations. Pyrolysis of plastic can provide solutions for problems created by plastic waste and give alternative fuel source for sustainable future.
With plastics being used more often in a variety of industries and leading to an increase in plastic trash, plastic pollution has become a major environmental concern on a global scale [70]. The environmental effects of traditional plastic waste management techniques such as landfilling and incineration, as well as their limited ability to handle non-recyclable plastics, present serious issues. One viable and long-term approach to managing plastic trash is the pyrolysis of plastic, which yields waste plastic oil (Figure 2) [71]. Pyrolysis is a useful technique for managing non-recyclable plastics, keeping them out of the ocean or landfills. In doing so, plastic pollution is lessened, resolving a critical environmental issue. Pyrolysis is a process that converts waste plastic into waste plastic oil, recovering important resources that would otherwise be wasted [72]. This is in line with the circular economy’s tenets, which minimize the need for virgin resources by recycling and reusing products. The creation and application of effective and affordable technology is essential to the success of plastic pyrolysis. To improve the pyrolysis process’s technical elements, further study is needed. Although pyrolysis has environmental advantages, it is important to consider any potential negative effects on the environment that may arise from the process, such as emissions and the handling of solid leftovers [19]. Strict adherence to environmental laws and the use of cutting-edge technologies can assist in reducing these worries. The cost of the technology, the availability of feedstock, and the market demand for the final products are some of the variables that determine pyrolysis’s economic feasibility. The viability of plastic pyrolysis projects can be increased with sustained technological breakthroughs and favorable economic conditions [73].
Products obtained after the plastic pyrolysis process: pyrolyzed gas, waste plastic oil and biochar
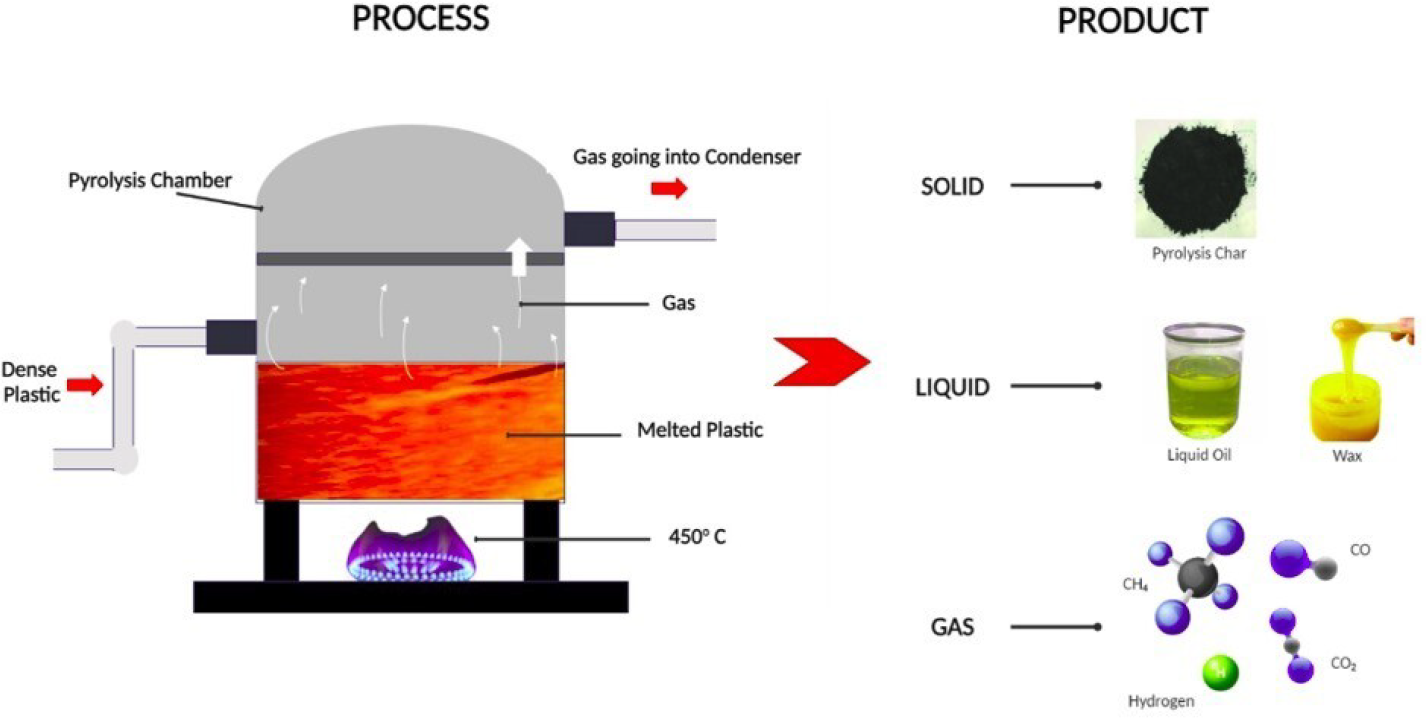
Waste plastic that has been gathered from different sources is sorted before being ready for the pyrolysis reactor. Increasing the effectiveness of the pyrolysis process can entail chopping or shredding the polymers. The pyrolysis reactor, which is heated to high temperatures, receives the prepared plastic trash [70]. The thermal breakdown of plastic into various compounds is facilitated by the absence of oxygen, which also inhibits combustion. Plastic pyrolysis yields solid wastes such as char or carbon black, liquid waste plastic oil, and syngas as its main products [74]. While there are potential uses for each of these items, the recovery and usage of waste plastic oil is the main focus here. Pyrolysis diverts nonrecyclable plastics from landfills and the ocean, offering a practical way to reduce plastic pollution. This procedure is in line with the need to lessen the negative effects of plastic waste on ecosystems and the environment. The process of producing waste plastic oil exemplifies the recovery, recycling, and reuse of materials - a circular economy [75]. Pyrolysis helps close the loop on plastic usage by turning waste plastic into a useful resource and lowering dependency on virgin resources. There is a market for waste plastic oil as a feedstock for many businesses. Because of its adaptability, it can be used as a feedstock for chemicals, a fuel source, or even as a step before new polymers are created. In industries looking for sustainable alternatives, this opens up business prospects [76]. The establishment of pyrolysis facilities for the manufacture of waste plastic oil creates job opportunities in plant operations, maintenance, logistics, and R&D. In addition to addressing environmental issues, this promotes regional economic growth. Refined waste plastic oil produced by pyrolysis can be used as a substitute energy source [3]. The burning of plastic oil may generate power as well as heat, which makes it a sustainable and renewable alternative to traditional fossil fuels. The inclusion of waste plastic oil in the energy mix helps diversify the sources of energy. Reducing reliance on traditional fossil fuels and building a more robust and sustainable energy infrastructure requires this diversification [77].
Plastic garbage comes from several sources and is first sorted and prepared. This could entail chopping or shredding to make the next steps of the pyrolysis process easier. After that, the ready-made plastic trash is put into a reactor for pyrolysis [78]. The thermal breakdown of the plastic starts by heating the reactor to high temperatures, usually between 400 and 800 °C. A comparison of waste plastic pyrolysis oil and conventional fuel is presented in Table 3. Three main products are obtained from the pyrolysis process: liquid waste plastic oil, char or carbon black (a solid residue), and syngas (a combination of hydrogen and carbon monoxide) [79]. Potential uses of waste plastic oil are highlighted in the context of energy production. Reducing the dependency on traditional fossil fuels through the use of waste plastic oil as a fuel source helps create a more environmentally friendly and sustainable energy mix [1]. Although waste plastic oil combustion results in carbon dioxide emissions, this method of disposal is more environmentally friendly than burning conventional plastics or using fossil fuels exclusively. Because plastic pyrolysis is a closed-loop process, it can reduce greenhouse gas emissions from the manufacture and disposal of plastic [62]. Waste plastic oil may be used as a fuel source for transportation, power generation, and industrial activities. Because of its adaptability, it can be integrated into the current energy infrastructure, opening up business prospects across other industries. The establishment of pyrolysis facilities for energy production results in job possibilities related to manufacturing, maintenance, and operations. The expansion of the waste plastic oil sector has supported sustainability and economic prosperity [80].
Fuel properties of waste plastic pyrolysis oil and comparison with those of conventional fuels
Fuel Properties | Waste Plastic Oil types | Commercial fuels | ||||||
---|---|---|---|---|---|---|---|---|
PET [38], [81] | HDPE [82] | PVC [38], [83] | LDPE [84] | PP [82] |
PS |
Gasoline (Petrol) [87] | Diesel | |
Calorific values (MJ/kg) | 28.2 | 40.5 | 21.1 | 39.5 | 40.8 | 43.0 | 42.5 | 43 |
Density at 15 °C (g/cm3) | 0.90 | 0.89 | 0.84 | 0.78 | 0.86 | 0.85 | 0.78 | 0.80 |
Ash (Wt%) | na | 0.0 | 0.0 | 0.02 | 0.0 | 0.006 | na | 0.01 |
Flash point (°C) | na | 48 | 40 | 41 | 30 | 26.1 | 42 | 52 |
Novel and sustainable methods for managing plastic waste are desperately needed as the global problem of plastic pollution grows. The process of pyrolysis converting plastic into waste plastic oil is a viable option for solving the problem of plastic waste and paves the way for the generation of sustainable energy [88]. It also yields waste plastic oil and helps maintain a closed-loop carbon cycle. In contrast to conventional plastic disposal techniques such as incineration, which release carbon stored in fossil fuels into the atmosphere, pyrolysis converts plastic into a valuable resource without adding more carbon to the environment. This closed-loop strategy aids in reducing the overall increase in greenhouse gas emissions [37]. Plastic trash can undergo anaerobic breakdown in landfills, releasing methane, a powerful greenhouse gas. This method helps prevent methane emissions and lowers overall greenhouse gas emissions by removing plastic from landfills. Carbon dioxide and other pollutants are released into the atmosphere during the incineration of plastic waste. Pyrolysis produces waste plastic oil with fewer emissions than incineration does, offering an option. This approach has the potential to lessen the carbon footprint caused by the disposal of plastic and improve air quality. Pyrolysis waste plastic oil has the potential to be a sustainable energy source [26]. Because of its adaptability, it can be used in a variety of industries, including transportation, industrial operations, and power generation. Waste plastic oil has the potential to increase in value as a marketable good as the demand for renewable energy sources increases. Facilities for the pyrolysis of waste plastic to produce waste oil are established and run, which leads to job possibilities in maintenance, research and development, and plant operations. This helps local economies and encourages expansion in the renewable energy industry. The energy mix can be made less dependent on conventional fossil fuels by including waste plastic oil. By addressing issues related to energy security and the environment, this diversification helps to create a more robust and sustainable energy infrastructure. Waste plastic oil might have lower carbon intensity than some traditional fossil fuels do. Pyrolysis is a potentially cleaner alternative because of its closed-loop carbon cycle, which guarantees that the carbon released during burning was previously stored during the formation of the plastic feedstock [89].
Plastic pyrolysis signifies a change from a linear, throwaway model to a circular economy strategy. Pyrolysis allows valuable resources to be recovered from plastic waste, converting it into waste plastic oil, a versatile and renewable feedstock, rather than being thrown away [90]. Unlike conventional plastic disposal techniques, which facilitate unidirectional material flow, pyrolysis creates a closed-loop system. By obtaining waste plastic oil through pyrolysis, one can minimize the need for virgin materials and lessen the impact on the environment by using this important resource for future applications. Pyrolysis waste plastic oil is a sustainable substitute for conventional fossil fuels [90]. There is a considerable decrease in the use of nonrenewable resources when this renewable resource is included in the energy mix, which lessens the impact on the environment and promotes the switch to cleaner energy sources. When waste plastic oil is burned, its carbon footprint is expected to be smaller than that of traditional fossil fuels [91]. By closing the carbon loop and lowering net greenhouse gas emissions, waste plastic oil helps replenish the carbon stored by the plastic feedstock during its initial growth [92]. By producing waste plastic oil, renewable energy sources can enter new markets. Waste plastic oil can be used as a feedstock by industries looking for greener options, opening up business opportunities and spurring innovation in the energy sector. Job opportunities in areas such as facility operation, maintenance, and research and development are created by the establishment and operation of pyrolysis facilities. In addition to helping the community at large, this promotes expansion in the green and sustainable energy industry [90].
The circular economy strategy, which replaces the linear “take, make, dispose” model, is exemplified by the pyrolysis process. A valuable resource is recovered by turning plastic garbage into waste plastic oil, which lowers the need for virgin materials and encourages a more sustainable material lifetime [93]. Pyrolysis turns waste plastics into reusable feedstock, creating a closed-loop system. A circular economy uses the waste plastic oil generated to promote a more regenerative and sustainable material flow. Pyrolysis waste plastic oil is a sustainable substitute for conventional fossil fuels [94]. This change contributes to a more sustainable energy landscape by reducing reliance on limited and harmful resources. When waste plastic oil is used to produce energy instead of traditional fossil fuels, the carbon footprint is reduced [95]. Pyrolysis is a closed-loop process that efficiently reduces net greenhouse gas emissions by sequestering carbon. Pyrolysis-derived waste plastic oil provides a flexible substitute fuel source. Its use is widespread throughout many industries, such as transportation, power generation, and industrial processes, adding to a resilient and diverse energy mix [96]. Energy security is increased by incorporating waste plastic oil into the energy mix since it decreases the dependency on a single source. Because of this diversification, stability is guaranteed even in the face of supply chain interruptions and geopolitical unpredictability related to conventional energy sources [97]. Recycled plastic oil is a growing sector of environmentally friendly energy. The market for waste plastic oil can be driven by industries looking for greener options, which will increase business prospects and encourage the growth of the renewable energy sector [98]. Job opportunities in maintenance, research and development, and facility management are created by the construction and running of pyrolysis facilities for the manufacture of waste plastic oil [99]. Local economies are bolstered, and knowledge of sustainable techniques is fostered.
To meet the growing need for sustainable energy sources as well as the environmental problems of plastic pollution, the pyrolysis of plastic has emerged as a promising green alternative. In addition to its function in energy generation, this technique has great promise for sophisticated recycling [100]. The pyrolysis of waste plastic oil produces a sustainable substitute for traditional fossil fuels. Through the utilization of plastic trash as a source of energy, this approach helps lessen the dependency on limited and harmful fossil fuels [101]. Reusing plastic oil to produce electricity is a way to reduce greenhouse gas emissions. The closed-loop pyrolysis process, in which carbon is released during burning and stored during the plastic development phase, contributes to the creation of more environmentally friendly and carbon-neutral energy [100]. By converting plastic garbage into useful waste plastic oil through pyrolysis, a closed-loop recycling system is created. By ensuring that plastic materials are reused, this closed loop lessens the demand for the manufacturing of virgin plastic and the total environmental effect of plastic usage. Pyrolysis-produced waste plastic oil has the potential to be used as a feedstock for the creation of new plastics. The molecular components of waste plastic oil can be purified by cutting-edge recycling techniques to produce premium plastic materials, which will help to develop a more circular and sustainable plastic economy [90], [102]. A developing industry for renewable energy is waste plastic oil. The demand for waste plastic oil can be fueled by industries looking for greener options, which will open up business prospects and propel the renewable energy industry forward.
The present review provides a brief overview of the pyrolysis of each type of plastic and its properties, optimized liquid oil yield, and technoeconomic evolution. Hence, pyrolysis is preferred by many researchers because of its ability to convert more plastic energy into usable products such as char, oil, and gaseous products. As a result, it is the finest option for waste plastic conversion and the most cost-effective option in terms of operation. Its versatility in product choice might be accomplished by altering the constraints correspondingly. Pyrolysis can be performed via either thermal or catalytic techniques. Therefore, the selection of the correct catalyst and the pyrolysis process produced can reduce the optimum operating working temperature with very high productivity of pyrolyzed oil compared with that of most polymers. The process induces sustainability, with a given amount of plastic waste produced in each country in tonnes. The pyrolysis process improves waste handling by using less landfill capacity, generating fewer pollutants, and being less expensive. Furthermore, with the availability of pyrolysis approaches for decomposing plastic waste into useful primary fuel, the dependency on nonrenewable fossil fuels may be minimized, increasing the energy demand.
The authors thank JSS AHER for providing financial support and laboratory facilities for this work.
Plastics waste management in Europe ,Makromolekulare Chemie. Macromolecular Symposia , Vol. 57 (1),pp 15–31 , 1992, https://doi.org/https://doi.org/10.1002/MASY.19920570104
, Plastic waste as pyrolysis feedstock for plastic oil production: A review ,Science of The Total Environment , Vol. 877 ,pp 162719 , 2023, https://doi.org/https://doi.org/10.1016/J.SCITOTENV.2023.162719
, Pyrolysis of plastic waste for liquid fuel production as prospective energy resource ,IOP Conf Ser Mater Sci Eng , Vol. 334 (1),pp 012001 , 2018, https://doi.org/https://doi.org/10.1088/1757-899X/334/1/012001
, - , A review on pyrolysis of plastic wastes, 2016
Plastic Waste Degradation in Landfill Conditions: The Problem with Microplastics, and Their Direct and Indirect Environmental Effects ,Int J Environ Res Public Health , Vol. 19 (20), 2022, https://doi.org/https://doi.org/10.3390/IJERPH192013223
, Focus on potential environmental issues on plastic world towards a sustainable plastic recycling in developing countries ,International Journal of Industrial Chemistry , Vol. 4 (1),pp 34 , 2013, https://doi.org/https://doi.org/10.1186/2228-5547-4-34
, Plastic Waste Degradation in Landfill Conditions: The Problem with Microplastics, and Their Direct and Indirect Environmental Effects ,Int J Environ Res Public Health , Vol. 19 (20),pp 13223 , 2022, https://doi.org/https://doi.org/10.3390/IJERPH192013223
, Production, use, and fate of all plastics ever made ,Sci Adv , Vol. 3 (7), 2017, https://doi.org/https://doi.org/10.1126/SCIADV.1700782/SUPPL_FILE/1700782_SM.PDF
, - , Plastic Waste Management: Current Status and Weaknesses, Handbook of Environmental Chemistry, 2022
Closing the loop on plastic packaging materials: What is quality and how does it affect their circularity? ,Science of the Total Environment , Vol. 630 ,pp 1394–1400 , 2018, https://doi.org/https://doi.org/10.1016/j.scitotenv.2018.02.330
, (Micro)plastic crisis: Un-ignorable contribution to global greenhouse gas emissions and climate change ,J Clean Prod , Vol. 254 ,pp 120138 , 2020, https://doi.org/https://doi.org/10.1016/J.JCLEPRO.2020.120138
, A comprehensive study of renewable energy sources: Classifications, challenges and suggestions ,Energy Strategy Reviews , Vol. 43 , 2022, https://doi.org/https://doi.org/10.1016/J.ESR.2022.100939
, Recent Advances in Polymer Recycling: A Short Review ,Curr Org Synth , Vol. 14 (2),pp 171–185 , 2017, https://doi.org/https://doi.org/10.2174/1570179413666160929095017
, Feedstock Recycling via Waste Plastic Pyrolysis ,Journal of the Japan Petroleum Institute , Vol. 59 (6),pp 243–253 , 2016, https://doi.org/https://doi.org/10.1627/JPI.59.243
, Pyrolysis of plastic waste for production of heavy fuel substitute: A techno-economic assessment ,Energy , Vol. 149 ,pp 865–874 , 2018, https://doi.org/https://doi.org/10.1016/j.energy.2018.02.094
, Pyrolysis of plastic species: A review of resources and products ,J Anal Appl Pyrolysis , Vol. 159 ,pp 105295 , 2021, https://doi.org/https://doi.org/10.1016/J.JAAP.2021.105295
, Review and Design Overview of Plastic Waste-to-Pyrolysis Oil Conversion with Implications on the Energy Transition ,Journal of Energy , Vol. 2023 (1),pp 1821129 , 2023, https://doi.org/https://doi.org/10.1155/2023/1821129
, Pyrolysis Kinetics of Polypropylene and High Density Polyethylene Wastes Using Kaolin Catalyst ,Materials Science Forum , Vol. 998 ,pp 114–119 , 2020, https://doi.org/https://doi.org/10.4028/WWW.SCIENTIFIC.NET/MSF.998.114
, A review on pyrolysis of plastic wastes ,Energy Convers Manag , Vol. 115 ,pp 308–326 , 2016, https://doi.org/https://doi.org/10.1016/J.ENCONMAN.2016.02.037
, - , A review on catalytic pyrolysis of plastic wastes to high-value products, 2022
- , Pyrolysis of polyolefin plastic waste and potential applications in asphalt road construction: A technical review, 2022
Catalytic stepwise pyrolysis of packaging plastic waste ,J Anal Appl Pyrolysis , Vol. 96 ,pp 54–62 , 2012, https://doi.org/https://doi.org/10.1016/J.JAAP.2012.03.004
, Catalytic pyrolysis of plastic waste: A review ,Process Safety and Environmental Protection , Vol. 102 ,pp 822–838 , 2016, https://doi.org/https://doi.org/10.1016/J.PSEP.2016.06.022
, Valorization of Plastic Waste to Generate Hydrocarbons by Hybrid Pyrolysis ,Environ Eng Sci , Vol. 39 (7),pp 662–670 , 2022, https://doi.org/https://doi.org/10.1089/ees.2021.0437
, Bio-fuels from thermochemical conversion of renewable resources: A review ,Renewable and Sustainable Energy Reviews , Vol. 12 (2),pp 504–517 , 2008, https://doi.org/https://doi.org/10.1016/J.RSER.2006.07.014
, Energy recovery from pyrolysis of plastic waste: Study on non-recycled plastics (NRP) data as the real measure of plastic waste ,Energy Convers Manag , Vol. 148 ,pp 925–934 , 2017, https://doi.org/https://doi.org/10.1016/J.ENCONMAN.2017.06.046
, A review on co-pyrolysis of biomass: An optional technique to obtain a high-grade pyrolysis oil ,Energy Convers Manag , Vol. 87 ,pp 71–85 , 2014, https://doi.org/https://doi.org/10.1016/J.ENCONMAN.2014.07.007
, Pyrolysis of mixtures of palm shell and polystyrene: An optional method to produce a high-grade of pyrolysis oil ,Environ Prog Sustain Energy , Vol. 33 (3),pp 1026–1033 , 2014, https://doi.org/https://doi.org/10.1002/EP.11850
, Thermogravimetry as a tool to classify waste components to be used for energy generation ,J Anal Appl Pyrolysis , Vol. 71 (2),pp 883–900 , 2004, https://doi.org/https://doi.org/10.1016/j.jaap.2003.12.001
, Catalytic efficiency of some novel nanostructured heterogeneous solid catalysts in pyrolysis of HDPE ,Polym Degrad Stab , Vol. 98 (12),pp 2512–2519 , 2013, https://doi.org/https://doi.org/10.1016/j.polymdegradstab.2013.09.009
, A Study on the Pyrolysis Characteristics of Poly(vinyl chloride) ,Journal of the Korean Institute of Chemical Engineers , Vol. 37 (4),pp 515–521 ,
, Study on pyrolysis characteristics of refuse plastic fuel using lab-scale tube furnace and thermogravimetric analysis reactor ,J Anal Appl Pyrolysis , Vol. 97 ,pp 29–38 , 2012, https://doi.org/https://doi.org/10.1016/J.JAAP.2012.06.009
, Pyrolysis of a fraction of waste polypropylene and polyethylene for the recovery of BTX aromatics using a fluidized bed reactor ,Fuel Processing Technology , Vol. 91 (3),pp 277–284 , 2010, https://doi.org/https://doi.org/10.1016/J.FUPROC.2009.10.009
, - , Determination of Physical and Chemical Characteristics of Electronic Plastic Waste (Ep-Waste) Resin Using Proximate and Ultimate Analysis Method, ICCBT 2008, 2008
AN OVERVIEW ON PYROLYSIS OF PLASTIC TRASHES ,An International Multidisciplinary ResearchJournal , Vol. 11 ,pp 1015–1022 , 2021, https://doi.org/https://doi.org/10.5958/2249-7137.2021.02196.0
, Transport fuel from waste plastics pyrolysis – A review on technologies, challenges and opportunities ,Energy Convers Manag , Vol. 258 ,pp 115451 , 2022, https://doi.org/https://doi.org/10.1016/J.ENCONMAN.2022.115451
, A review of pyrolysis technologies and feedstock: A blending approach for plastic and biomass towards optimum biochar yield ,Renewable and Sustainable Energy Reviews , Vol. 167 ,pp 112715 , 2022, https://doi.org/https://doi.org/10.1016/J.RSER.2022.112715
, - , Utilization of Two Different Types of Plastic Wastes from Daily and Industrial Life, 2013
Predicting pyrolysis products of PE, PP, and PET using NRTL activity coefficient model ,J Chem , 2013, https://doi.org/https://doi.org/10.1155/2013/487676
, Recovery of hydrocarbon liquid from waste high density polyethylene by thermal pyrolysis ,Brazilian Journal of Chemical Engineering , Vol. 28 (4),pp 659–667 , 2011, https://doi.org/https://doi.org/10.1590/S0104-66322011000400011
, Pyrolysis Study of Polypropylene and Polyethylene Into Premium Oil Products ,Int J Green Energy , Vol. 12 (7),pp 663–671 , 2015, https://doi.org/https://doi.org/10.1080/15435075.2014.880146
, Thermal and catalytic pyrolysis of polyethylene over HZSM5 and HUSY zeolites in a batch reactor under dynamic conditions ,Appl Catal B , Vol. 86 (1–2),pp 78–86 , 2009, https://doi.org/https://doi.org/10.1016/J.APCATB.2008.07.026
, Pyrolysis of high-density polyethylene in a fluidised bed reactor. Influence of the temperature and residence time ,J Anal Appl Pyrolysis , Vol. 63 (1),pp 1–15 , 2002, https://doi.org/https://doi.org/10.1016/S0165-2370(01)00137-1
, Vacuum pyrolysis of PVC I. Kinetic study ,Polym Degrad Stab , Vol. 64 (1),pp 127–144 , 1999, https://doi.org/https://doi.org/10.1016/S0141-3910(98)00186-4
, An analysis of barriers for plastic recycling in the Indian plastic industry ,Benchmarking , Vol. 24 (2),pp 415–430 , 2017, https://doi.org/https://doi.org/10.1108/BIJ-11-2014-0103/FULL/XML
, Dechlorination of fuels in pyrolysis of PVC containing plastic wastes ,Fuel Processing Technology , Vol. 92 (2),pp 253–260 , 2011, https://doi.org/https://doi.org/10.1016/J.FUPROC.2010.05.008
, Degradation and Stabilization of Low-density Polyethylene Films used as Greenhouse Covering Materials ,Journal of Agricultural Engineering Research , Vol. 76 (4),pp 309–321 , 2000, https://doi.org/https://doi.org/10.1006/JAER.1999.0513
, - , Tribology of natural fiber polymer composites, 2008
Catalytic pyrolysis of polyethylene ,J Anal Appl Pyrolysis , Vol. 63 (1),pp 29–41 , 2002, https://doi.org/https://doi.org/10.1016/S0165-2370(01)00139-5
, Thermal and catalytic degradation of structurally different types of polyethylene into fuel oil ,Polym Degrad Stab , Vol. 56 (1),pp 37–44 , 1997, https://doi.org/https://doi.org/10.1016/S0141-3910(96)00191-7
, Feedstock recycling of polyethylene in a two-step thermo-catalytic reaction system ,J Anal Appl Pyrolysis , Vol. 79 (1–2),pp 415–423 , 2007, https://doi.org/https://doi.org/10.1016/J.JAAP.2006.11.008
, Composition of products from the pyrolysis of polyethylene and polystyrene in a closed batch reactor: Effects of temperature and residence time ,J Anal Appl Pyrolysis , Vol. 86 (2),pp 293–303 , 2009, https://doi.org/https://doi.org/10.1016/j.jaap.2009.07.008
, Polypropylene as a Promising Plastic: A Review ,American Journal of Polymer Science , 2016, https://doi.org/https://doi.org/10.5923/j.ajps.20160601.01
, Degradation of polyethylene and polypropylene into fuel oil by using solid acid and non-acid catalysts ,J Anal Appl Pyrolysis , Vol. 51 (1),pp 135–155 , 1999, https://doi.org/https://doi.org/10.1016/S0165-2370(99)00013-3
, Pyrolysis of municipal plastic wastes for recovery of gasoline-range hydrocarbons ,J Anal Appl Pyrolysis , Vol. 72 (1),pp 97–102 , 2004, https://doi.org/https://doi.org/10.1016/J.JAAP.2004.03.001
, - ,
Pyrolysis of Polystyrene Waste: A Review ,Polymers (Basel) , Vol. 13 (2),pp 225 , 2021, https://doi.org/https://doi.org/10.3390/polym13020225 - , Polystyrene: Synthesis, Production and Applications, 2000
Pyrolysis of polystyrene waste in a fluidized-bed reactor to obtain styrene monomer and gasoline fraction ,Fuel Processing Technology , Vol. 63 (1),pp 45–55 , 2000, https://doi.org/https://doi.org/10.1016/S0378-3820(99)00066-1
, Pyrolysis of plastic waste: Opportunities and challenges ,J Anal Appl Pyrolysis , Vol. 152 , 2020, https://doi.org/https://doi.org/10.1016/j.jaap.2020.104804
, Pyrolysis of mixed plastics used in the electronics industry ,J Anal Appl Pyrolysis , Vol. 52 (2),pp 199–224 , 1999, https://doi.org/https://doi.org/10.1016/S0165-2370(99)00045-5
, Chemical recycling of mixed plastics of pyrolysis ,Advances in Polymer Technology , Vol. 14 (4),pp 337–344 , 1995, https://doi.org/https://doi.org/10.1002/adv.1995.060140407
, Thermal degradation of mixed plastic waste to aromatics and gas ,Polym Degrad Stab , Vol. 53 (2),pp 189–197 , 1996, https://doi.org/https://doi.org/10.1016/0141-3910(96)00087-0
, Pyrolysis of polyolefins for increasing the yield of monomers’ recovery ,Waste Management , Vol. 32 (5),pp 840–846 , 2012, https://doi.org/https://doi.org/10.1016/J.WASMAN.2011.10.009
, Producing hydrocarbon fuel from the plastic waste: Techno-economic analysis ,Korean Journal of Chemical Engineering 2021 38:11 , Vol. 38 (11),pp 2208–2216 , 2021, https://doi.org/https://doi.org/10.1007/S11814-021-0876-3
, Techno-economic analysis of biomass fast pyrolysis to transportation fuels ,Fuel , Vol. 89 (1),pp S2–S10 , 2010, https://doi.org/https://doi.org/10.1016/J.FUEL.2010.07.029
, Techno-Economic Evaluation of High Temperature Pyrolysis Processes for Mixed Plastic Waste ,Chemical Engineering Research and Design , Vol. 76 (3),pp 427–439 , 1998, https://doi.org/https://doi.org/10.1205/026387698524857
, Techno-economic feasibility and flowsheet synthesis of scrap tire/plastic waste liquefaction ,Journal of Elastomers and Plastics , Vol. 31 (3),pp 232–254 , 1999, https://doi.org/https://doi.org/10.1177/009524439903100305
, Techno-economic assessment of thermo-chemical treatment (TCT) units in the Greater London area ,Chemical Engineering Journal , Vol. 248 ,pp 253–263 , 2014, https://doi.org/https://doi.org/10.1016/j.cej.2014.03.053
, A techno-economic comparison of fluidized bed gasification of two mixed plastic wastes ,Waste Management , Vol. 31 (7),pp 1494–1504 , 2011, https://doi.org/https://doi.org/10.1016/J.WASMAN.2011.02.004
, Plastic Waste: Challenges and Opportunities to Mitigate Pollution and Effective Management ,Int J Environ Res , Vol. 17 (1),pp 1–37 , 2023, https://doi.org/https://doi.org/10.1007/S41742-023-00507-Z/FIGURES/26
, Co-pyrolysis of biomass and waste plastics for production of chemicals and liquid fuel: A review on the role of plastics and catalyst types ,Arabian Journal of Chemistry , Vol. 16 (1),pp 104389 , 2023, https://doi.org/https://doi.org/10.1016/J.ARABJC.2022.104389
, Review and Design Overview of Plastic Waste-to-Pyrolysis Oil Conversion with Implications on the Energy Transition ,Journal of Energy , Vol. 2023 ,pp 1–25 , 2023, https://doi.org/https://doi.org/10.1155/2023/1821129
, Biodegradable plastic applications towards sustainability: A recent innovations in the green product ,Clean Eng Technol , Vol. 6 ,pp 100404 , 2022, https://doi.org/https://doi.org/10.1016/J.CLET.2022.100404
, Co-pyrolysis of biomass and different plastic waste to reduce hazardous waste and subsequent production of energy products: A review on advancement, synergies, and future prospects ,Renew Energy ,pp 120103 , 2024, https://doi.org/https://doi.org/10.1016/J.RENENE.2024.120103
, A comprehensive review on pyrolysis from the circular economy point of view and its environmental and social effects ,J Clean Prod , Vol. 388 ,pp 136021 , 2023, https://doi.org/https://doi.org/10.1016/J.JCLEPRO.2023.136021
, Retrieving back plastic wastes for conversion to value added petrochemicals: opportunities, challenges and outlooks ,Appl Energy , Vol. 345 ,pp 121307 , 2023, https://doi.org/https://doi.org/10.1016/J.APENERGY.2023.121307
, Review on biofuel production: Sustainable development scenario, environment, and climate change perspectives − A sustainable approach ,J Environ Chem Eng , Vol. 12 (2),pp 111996 , 2024, https://doi.org/https://doi.org/10.1016/J.JECE.2024.111996
, Catalytic pyrolysis of plastic waste: Moving toward pyrolysis based biorefineries ,Front Energy Res , Vol. 7 ,pp 437000 , 2019, https://doi.org/https://doi.org/10.3389/FENRG.2019.00027/BIBTEX
, Potential of pyrolysis processes in the waste management sector ,Thermal Science and Engineering Progress , Vol. 3 ,pp 171–197 , 2017, https://doi.org/https://doi.org/10.1016/J.TSEP.2017.06.003
, Pyrolysis technology for plastic waste recycling: A state-of-the-art review ,Prog Energy Combust Sci , Vol. 93 ,pp 101021 , 2022, https://doi.org/https://doi.org/10.1016/J.PECS.2022.101021
, Waste Polyethylene Terephthalate (PETE-1) Conversion into Liquid Fuel ,Ashdin Publishing Journal of Fundamentals of Renewable Energy and Applications , Vol. 1 , 2011, https://doi.org/https://doi.org/10.4303/jfrea/R101202
, Catalytic efficiency of some novel nanostructured heterogeneous solid catalysts in pyrolysis of HDPE ,Polym Degrad Stab , Vol. 98 (12),pp 2512–2519 , 2013, https://doi.org/https://doi.org/10.1016/j.polymdegradstab.2013.09.009
, Catalytic degradation of waste PVC into liquid fuel using baco 3 as catalyst and its blending properties with diesel fuel ,Discover ,pp 74–78 , 2014
, Production and Analysis of Pyrolysis oil from waste plastic in Kolhapur city ,International Journal of Engineering Research and General Science , Vol. 3 (1), 2015
, Pyrolysis of plastic wastes. 1. Effect of plastic waste composition on product yield ,J Anal Appl Pyrolysis , Vol. 51 (1–2),pp 39–55 , 1999, https://doi.org/https://doi.org/10.1016/S0165-2370(99)00007-8
, - , Composition of Liquid Fuels Derived from the Pyrolysis of Plastics, Feedstock Recycling and Pyrolysis of Waste Plastics: Converting Waste Plastics into Diesel and Other Fuels, 2006
Pyrolysis study of polypropylene and polyethylene into premium oil products ,Int J Green Energy , Vol. 12 (7),pp 663–671 , 2015, https://doi.org/https://doi.org/10.1080/15435075.2014.880146
, Plastics waste management: A review of pyrolysis technology ,Clean Technologies and Recycling 2021 1:50 , Vol. 1 (1),pp 50–69 , 2021, https://doi.org/https://doi.org/10.3934/CTR.2021003
, Pyrolytic Waste Plastic Oil and Its Diesel Blend: Fuel Characterization ,J Environ Public Health , Vol. 2016 , 2016, https://doi.org/https://doi.org/10.1155/2016/7869080
, Bioplastics for a circular economy ,Nature Reviews Materials 2022 7:2 , Vol. 7 (2),pp 117–137 , 2022, https://doi.org/https://doi.org/10.1038/s41578-021-00407-8
, Hydrogen Production Technologies: From Fossil Fuels toward Renewable Sources. A Mini Review ,Energy and Fuels , Vol. 35 (20),pp 16403–16415 , 2021, https://doi.org/https://doi.org/10.1021/ACS.ENERGYFUELS.1C02501/ASSET/IMAGES/LARGE/EF1C02501_0004.JPEG
, Plastics and climate change—Breaking carbon lock-ins through three mitigation pathways ,One Earth , Vol. 5 (4),pp 361–376 , 2022, https://doi.org/https://doi.org/10.1016/J.ONEEAR.2022.03.007
, - , Pyrolysis of polystyrene waste: A review, Jan. 2021, Multidisciplinary Digital Publishing Institute
- , Alternate Strategies for Conversion of Waste Plastic to Fuels, 2013, 2013
Economic and Environmental Assessment of Plastic Waste Pyrolysis Products and Biofuels as Substitutes for Fossil-Based Fuels ,Front Energy Res , Vol. 9 ,pp 676233 , 2021, https://doi.org/https://doi.org/10.3389/FENRG.2021.676233/BIBTEX
, Plastic Waste Management Strategies and Their Environmental Aspects: A Scientometric Analysis and Comprehensive Review ,Int J Environ Res Public Health , Vol. 19 (8), 2022, https://doi.org/https://doi.org/10.3390/IJERPH19084556
, - Energy Security and The Green Transition, 20242024, https://www.imf.org/en/Publications/WP/Issues/2024/01/12/Energy-Security-and-The-Green-Transition-543806
Sustainability of biodegradable plastics: New problem or solution to solve the global plastic pollution? ,Current Research in Green and Sustainable Chemistry , Vol. 5 ,pp 100273 , 2022, https://doi.org/https://doi.org/10.1016/J.CRGSC.2022.100273
, Plastics and climate change—Breaking carbon lock-ins through three mitigation pathways ,One Earth , Vol. 5 (4),pp 361–376 , 2022, https://doi.org/https://doi.org/10.1016/J.ONEEAR.2022.03.007
, Plastics recycling: challenges and opportunities ,Philosophical Transactions of the Royal Society B: Biological Sciences , Vol. 364 (1526),pp 2115 , 2009, https://doi.org/https://doi.org/10.1098/RSTB.2008.0311
, Pyrolysis technology for plastic waste recycling: A state-of-the-art review ,Prog Energy Combust Sci , Vol. 93 ,pp 101021 , 2022, https://doi.org/https://doi.org/10.1016/J.PECS.2022.101021
, Circular economy strategies for combating climate change and other environmental issues ,Environmental Chemistry Letters 2022 21:1 , Vol. 21 (1),pp 55–80 , 2022, https://doi.org/https://doi.org/10.1007/S10311-022-01499-6
,